INSIGHT
Electric spindle drive for the automation of mechanical vices without rotary feedthrough
A robot with an electric torque screwdriver is the perfect automation of milling machines without a rotary feedthrough
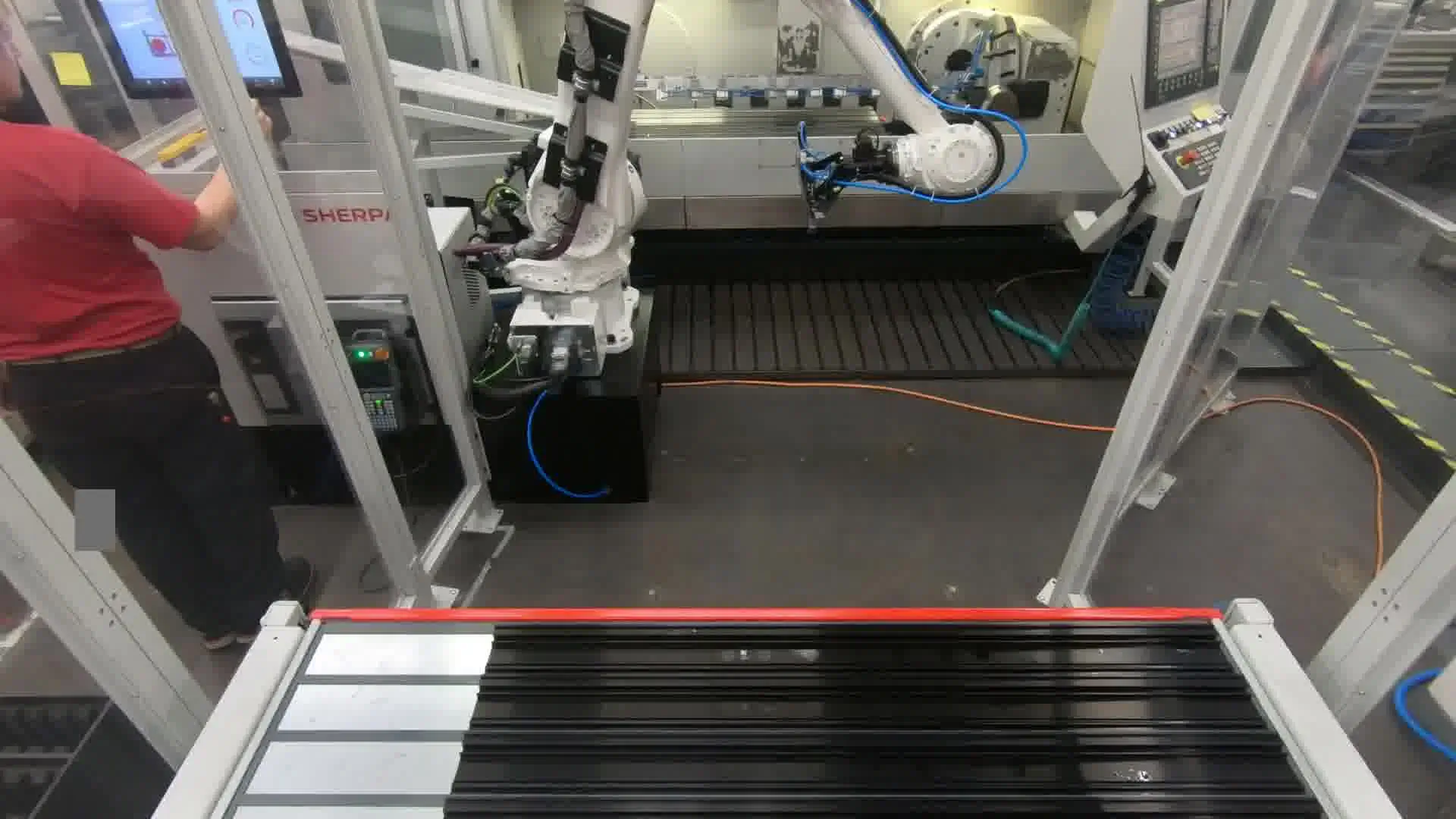

A robot with an electric torque screwdriver is
25 years ago, loading robots were
25 years ago, loading robots in machining were reserved for industries with large production batches, in short: primarily the automotive industry. For contract manufacturers with significantly lower quantities, circular and accumulation conveyors were the entry point into automation. More modern systems use robots to insert pallets or vices with zero-point clamping systems into CNC machines. The advantage of this is the low initial investment, which initially makes them attractive for small batch sizes - but only initially, because they quickly reach their limits as the number of units increases. On the one hand, a clamping system must be purchased for each individual component. On the other hand, vices of different sizes and in the appropriate number are required. This means that, over the product life cycle of the automation, the costs for vices usually exceed the purchase price of the handling system. For
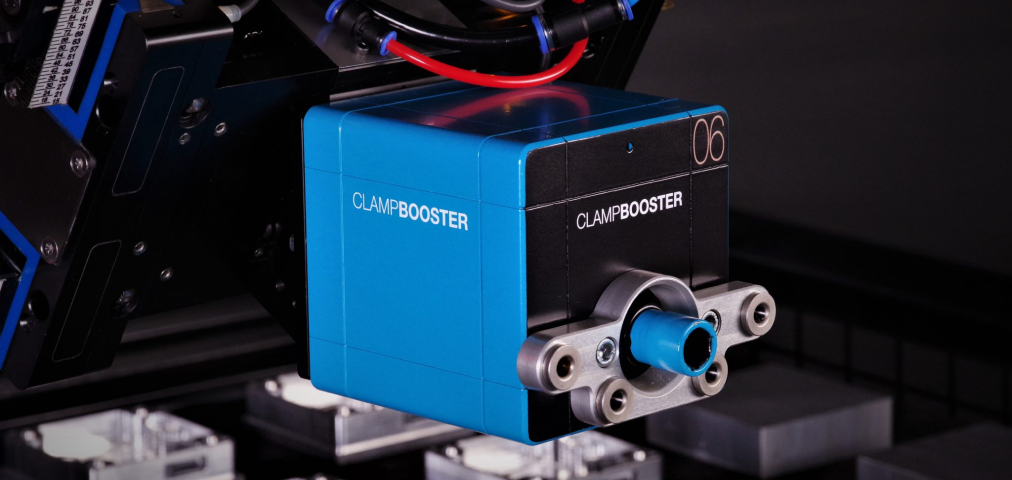
A robot with an electric torque screwdriver is
Vice with zero-point clamping system in CNC machines.
For robust use, the Stuttgart-based company SHERPA Robotics has seamlessly integrated the torque screwdriver into its loading robot SherpaLoader®. All process parameters such as clamping torque, opening path and clamping position are easy to configure using a touch panel and additional vices can be flexibly integrated. The symbiosis of SherpaLoader® and ClampBooster enables robot-assisted loading of a milling machine - without costly machine conversion - and allows manufacturers to continue using their familiar clamping system.
But the use of a robot offers further advantages, as it can pre-stamp workpieces automatically. Up to now, pre-stamping was always a manual work step - even with automated loading. A six-axis robot such as the SherpaLoader® can place components in a stamping station before clamping them in the processing machine, where they are given a contour in the clamping area that enables positive clamping in the machine vice. The smaller clamping area not only saves material and allows reduced clamping forces, but also optimizes access to the workpiece from all sides. This is particularly useful for 5-sided machining. SHERPA Robotics has reliably integrated this pre-stamping into the workpiece handling with the SOLIDStamp system from HWR Spanntechnik. Parallel to the main process, the robot places blanks in a stamping station before they are clamped in the vice of the processing machine.
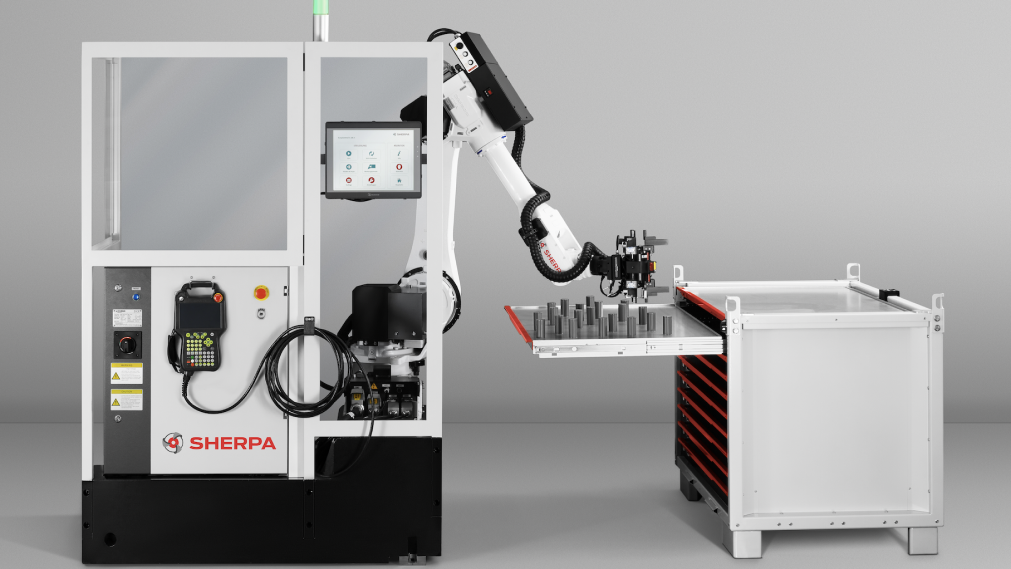
A robot with an electric torque screwdriver is
The CNC automation SherpaLoader® differs from conventional loading systems not only through the perfect integration of ClampBooster and SOLIDStamp embossing station, it also has another impressive feature: the 3D camera system. As a leading manufacturer of camera-supported CNC automation, SHERPA Robotics has been using camera systems since 2016 that allow the loading robot to recognize parts at any time of day or night. This means that the raw material can be provided on standard table trolleys or Euro pallets, without laser-cut sheet metal templates and without the setup effort that would be required with conventional systems. Drawer systems are available so that even short-run components can be manufactured unmanned for over 48 hours. This reduces manufacturing costs, especially for small to medium batch sizes, which gives a decisive competitive advantage. The SherpaLoader® product family is built in three sizes and for workpieces up to 70 kilograms. A variety of flexible extensions are also available, from stacking and cleaning to measuring and labeling.